From Concept to Operation in Six Weeks: Accelerated Ductwork Installation
We pride ourselves on delivering innovative, cost-effective solutions that drive real-world results for our clients. In this post, we highlight a project where our team was tasked with designing and implementing a custom ducting solution for a thermal oxidizer tie-in from an oven along with supply and discharge ducting to the oven cooling zone. Faced with tight deadlines and budget constraints, our integrated approach—combining visual design tools, precise planning, and streamlined installation—enabled the client to go from initial concept to full system operation in just under six weeks.
INITIAL DESIGN SUPERIMPOSED OVER THE PROCESS IMAGE
After obtaining the process area image, we designed the ducting system and over-layed the design on top of the image of the process area. This process allowed plant operations personnel to review the layout and suggest modifications to the design.
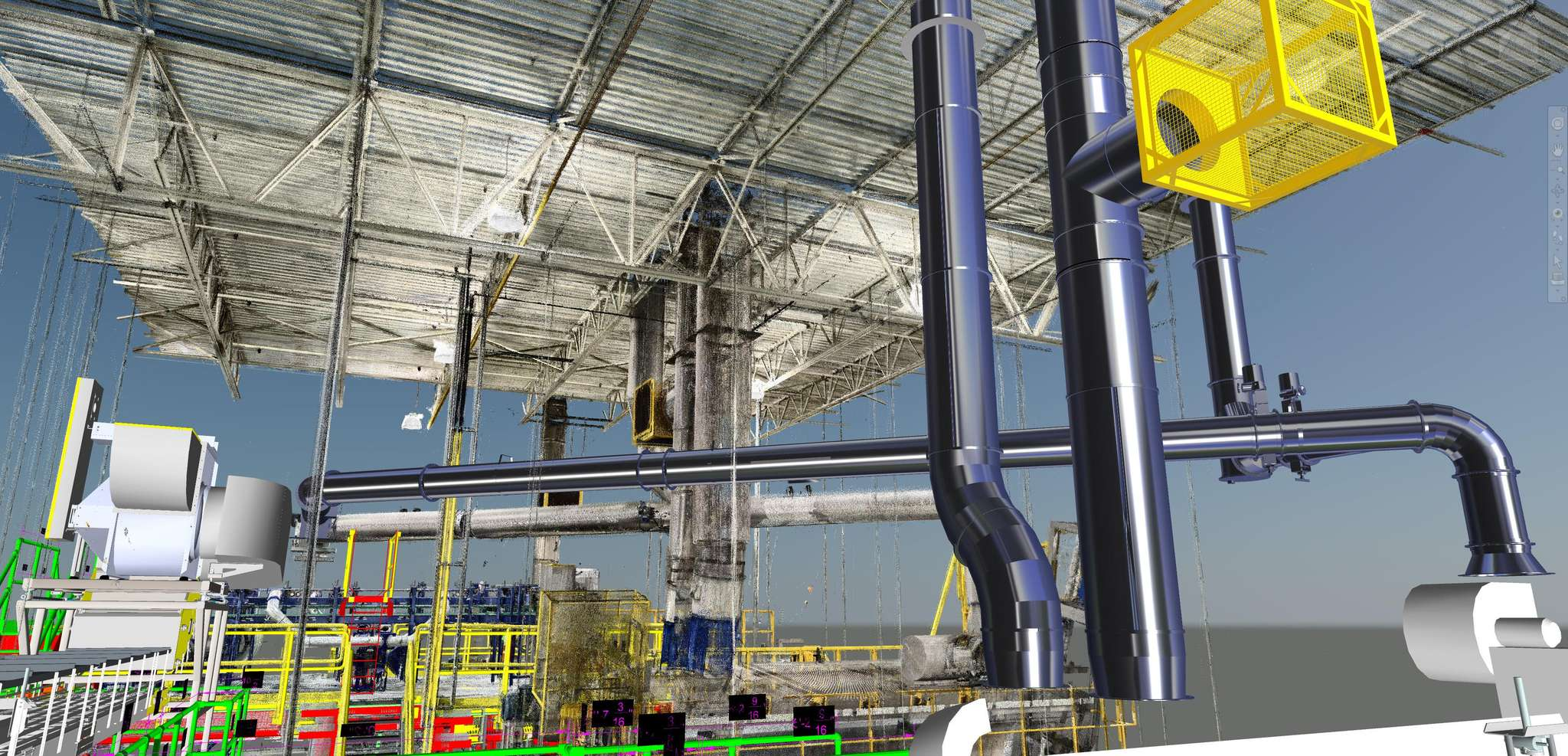
- The proposed system design and rendering allowed the end user to envision the installed system.
- This process ensured accuracy in the system quote because the precise part requirements were a part of the design.
- Our process could be used with any duct type – Euro-style (Noro) tubing, clamp-together rolled-lip duct, flanged ducting, or spiral duct.
ACCURATE ASSEMBLY DRAWING PRODUCED
Each part that is required for installation was called out on the assembly plan. This project included clamp-together duct, flanged duct, expansion joints, automatic butterfly valves, a fabricated air filter, roof curb caps, duct hangers and support collars, duct gaskets, and hardware.
- All parts were listed on the drawing bill of materials (BOM) and all parts were delivered in a kit to the job site.
- Delivery to the job site was consolidated into one shipment in order to eliminate the task of the contractor searching for parts.
- We published easy-to-follow, detailed assembly drawings that expedited the installation of the system.
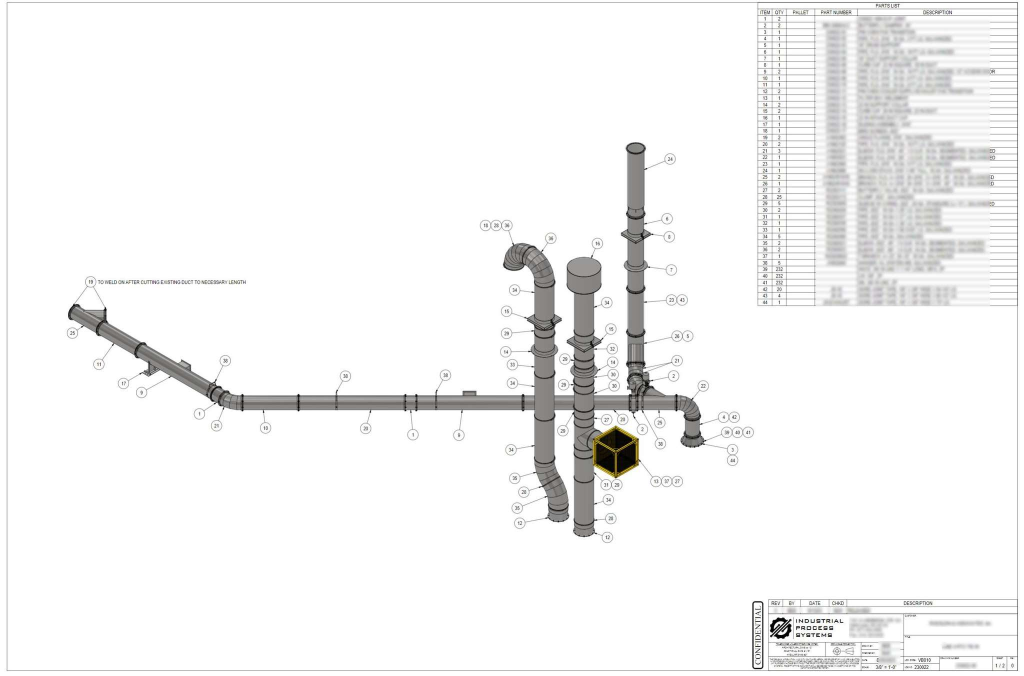
DETAILED DESIGN PROCESS YIELDED OPTIMIZED RESULTS
In the end, the results of this project were noteworthy.
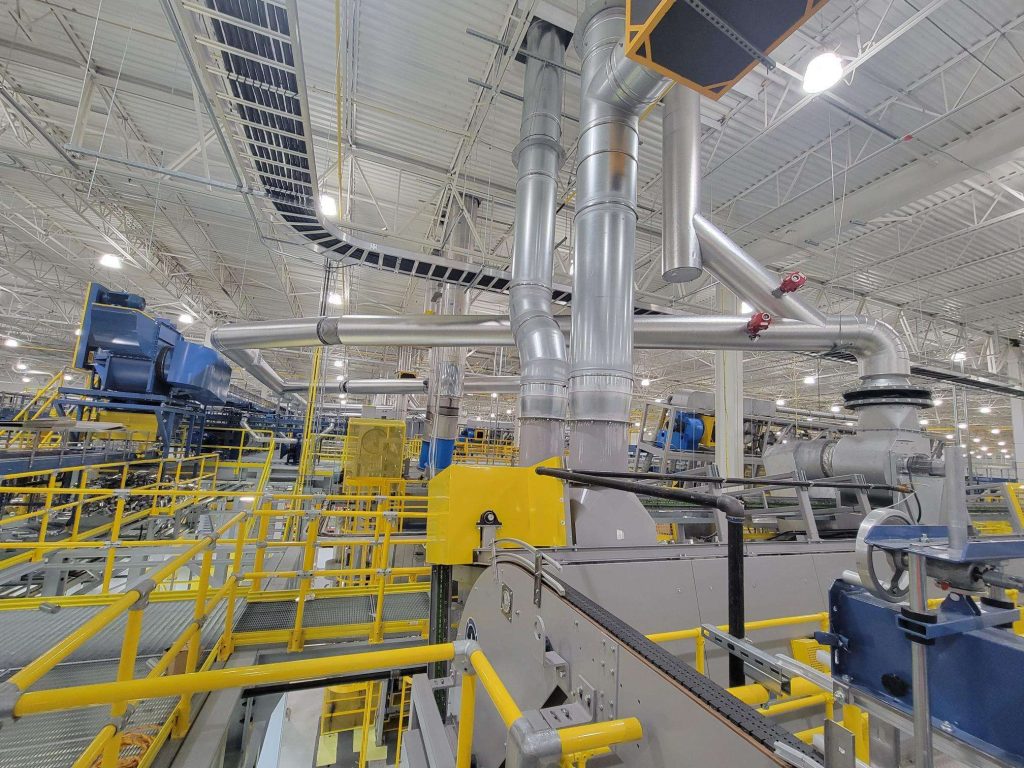
- No installation errors or contractor questions; this system was installed and in-operation before the client project engineer was even aware of it.
- There were no interferences from the ductwork with joists on roof stack penetrations
- The installation and system startup was completed in less than a week
- There was no wasted additional parts (just-in-case) that were shipped to the job site, only to be thrown away after system installation.
- There was no need for last-minute rush parts that needed to be shipped to the job site.
- The result was a total time of six (6) weeks from design start, through component fabrication, to fully installed system, startup, and into operation.
We’ve applied state-of-the-art technology to the process of designing, fabricating, and installing industrial ductwork systems. Using our process will enhance your up-front customer engagement, optimize your quote accuracy, expand your project capabilities, and increase your system sales.